Case Study: Transforming Operations with Peak Performance Data
Introduction to Peak Performance Data
In today's fast-paced business environment, leveraging data to drive efficiency and performance is no longer optional—it's essential. Companies are increasingly turning to data-driven solutions to optimize their operations and gain a competitive edge. One such approach is Peak Performance Data, a powerful tool that offers insights into operational efficiencies and inefficiencies.
This case study explores how a mid-sized manufacturing company transformed its operations by harnessing the power of Peak Performance Data. By focusing on key metrics and implementing strategic changes, the company achieved remarkable results.

Identifying Operational Challenges
The company faced several operational challenges that hindered productivity and profitability. These included fluctuating production times, inconsistent quality control, and high equipment downtime. Recognizing these issues, the management decided to adopt a data-centric approach to address them effectively.
By implementing Peak Performance Data, the company aimed to identify bottlenecks in its processes, streamline operations, and ensure consistent quality output. The initial step was gathering comprehensive data from various departments to pinpoint areas requiring immediate attention.
Data Collection and Analysis
To begin the transformation, the company installed sensors and monitoring equipment on its production lines. This technology collected real-time data on machine performance, production rates, and downtime incidents. The data was then analyzed using advanced analytics tools to uncover patterns and trends.
The analysis revealed several critical insights. For instance, it identified specific machines that frequently malfunctioned, causing significant delays. Additionally, it highlighted variations in production speed that contributed to inconsistent product quality.
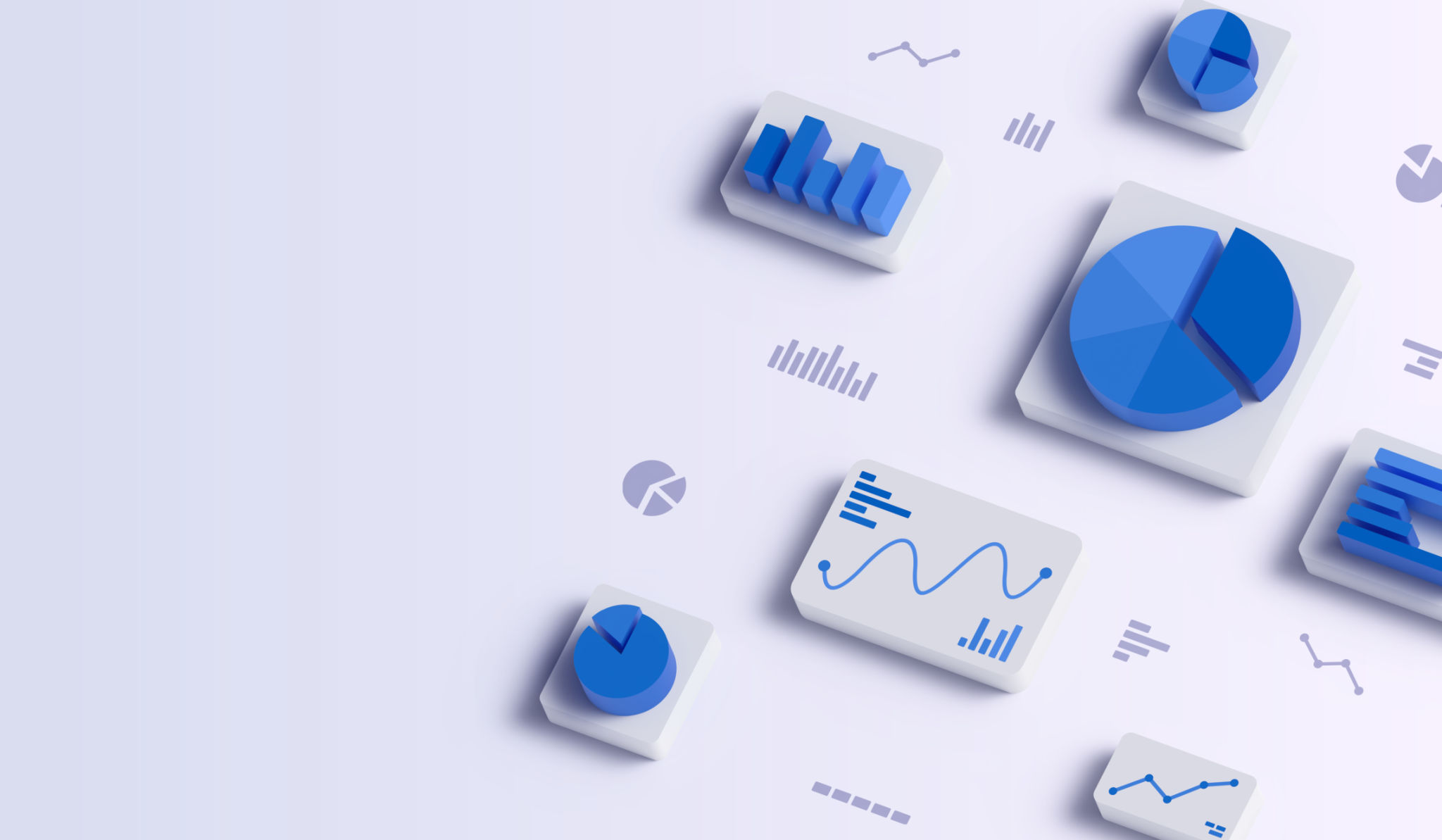
Implementing Strategic Changes
Armed with these insights, the company embarked on a strategic overhaul of its operations. Key changes included:
- Preventive Maintenance: Implementing a regular maintenance schedule for equipment to reduce unexpected breakdowns.
- Process Standardization: Establishing standardized procedures for production to minimize variations in quality.
- Employee Training: Conducting workshops and training sessions to ensure staff were well-versed in new technologies and processes.
These changes were strategically designed to address the root causes of inefficiencies identified through data analysis.
Results and Benefits
The transformation yielded significant improvements across the board. Production times decreased by 20%, while product quality consistency improved by 15%. Equipment downtime was reduced by an impressive 30%, directly contributing to increased productivity and reduced operational costs.
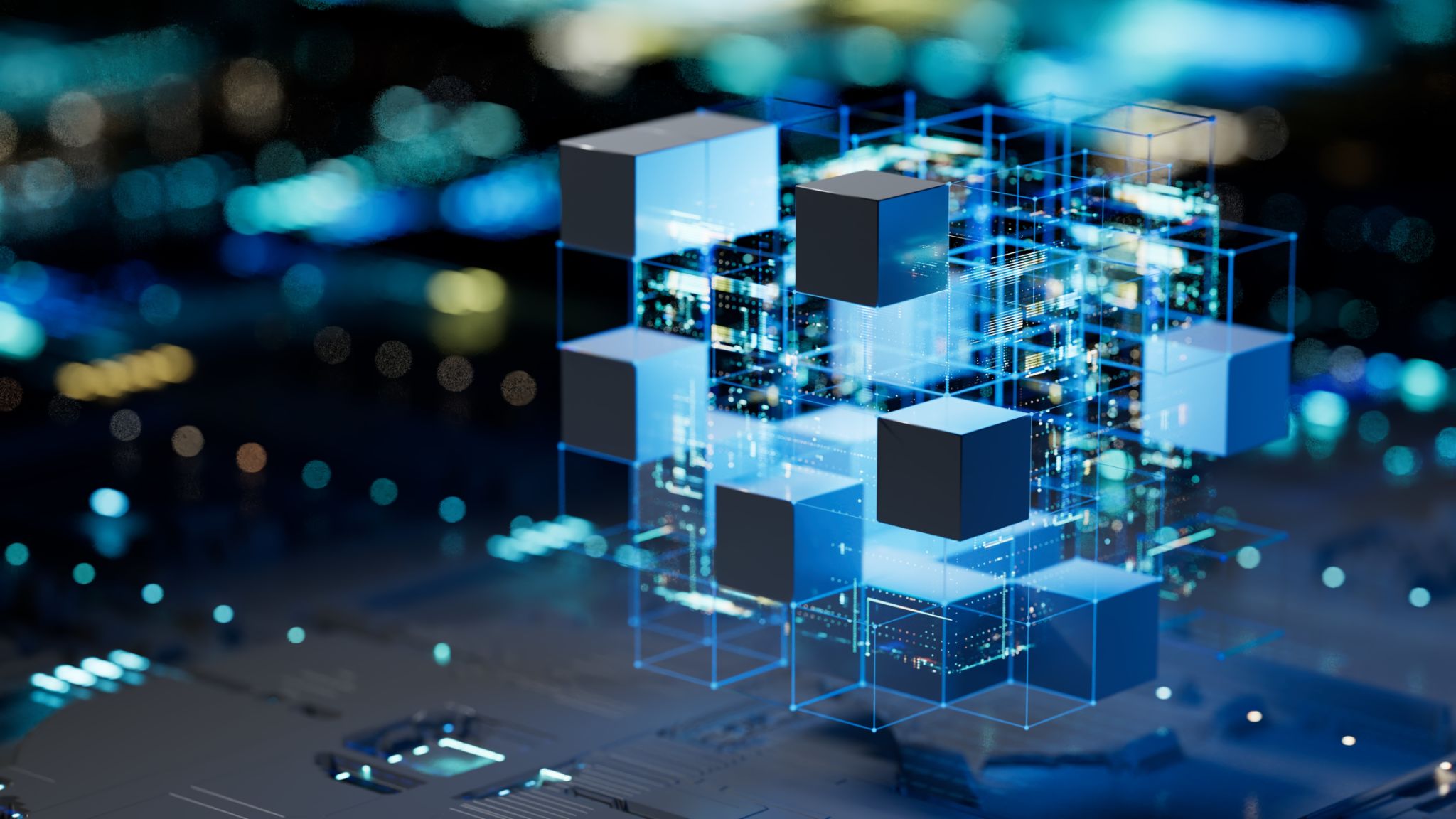
The company's commitment to leveraging Peak Performance Data not only optimized its operations but also fostered a culture of continuous improvement. Employees became more engaged as they saw tangible results from their efforts, further driving operational excellence.
Conclusion: A Model for Success
This case study highlights the transformative impact of Peak Performance Data on manufacturing operations. By focusing on data-driven insights, the company was able to overcome significant challenges and achieve substantial gains in efficiency and profitability.
For businesses seeking similar success, investing in data analytics and fostering a culture of continuous improvement are crucial steps. As demonstrated by this case, the strategic use of data can lead to sustainable competitive advantages in today's dynamic market landscape.